
The cost of such materials is directly traceable to each individual unit of product manufactured and is, therefore, regarded as direct or product cost. The quantity of direct materials needed to make a unit of product is usually known or can be closely estimated. For example, an engineer working in a furniture manufacturing company can easily tell you the quantity of wood, glue, nails and length of glass sheet needed to manufacture an executive table.
Safety Risks
This delay can result in lost revenue and increased costs, as employees may need to be paid for their time even if they cannot work. By distinguishing between direct and indirect materials, companies can better understand their actual production costs. Direct materials are easy to identify and track, and their cost can be directly attributed turbotax is open and accepting tax returns now to producing a specific product. Direct materials are those used in producing a final product, while indirect materials are not directly used in the production process but are necessary to support it. Understanding the difference between these two types of materials is vital for effective cost management and accurate accounting.
Which of these is most important for your financial advisor to have?
However, if the amount is significantly minor, the cost of these materials can be directly charged to expense as incurred during a period. The selection from the either approach is largely impacted by the entity’s costing policies. Whenever a business engages in product manufacturing, the process necessitates the use of both direct and indirect materials, further enhanced by efficient purchasing software. While both types play a vital role in influencing production costs and overall profitability, they diverge in several aspects. Finally, using technology to manage indirect materials can provide businesses with greater scalability. As a business grows, its indirect materials management needs may become more complex.
Indirect materials cost
- All manufacturing entities essentially use some kind of raw materials to manufacture their output.
- For example, disposable gloves, scissors, and cotton are instances of these materials in a healthcare unit.
- Inventory management software can help companies track inventory levels and automate reordering processes.
- For example, if the wrong type of lubricant is used, it can cause premature wear and tear on machinery, leading to breakdowns and downtime.
When the cost of materials or the amount of materials used are less than expected, this is a favorable direct materials variance. More and more companies are seeking suppliers prioritizing sustainability. Suppliers should commit to sustainable sourcing and manufacturing practices. They should also have a track record of reducing waste and minimizing environmental impact.
Would you prefer to work with a financial professional remotely or in-person?
Because so many of these materials are used in the manufacture of vehicles, it would be impossible for the company to allocate the cost of each bolt to the vehicle being produced. Suppliers should proactively introduce new and innovative products that can improve a company’s operations. They should be able to provide recommendations and solutions to help a company achieve its goals. Who knows what bolts will be used to produce what cars later in the manufacturing process.
Accounting for indirect materials
The materials used during production that are directly visible in the finished product are known as direct materials. They consist of the components, subcomponents, and raw materials required to produce a product. Since direct material costs can be quantified, they can be easily and precisely allocated to specific production or batch costs. Because they affect the price of a good or service, it is crucial to track and record the cost of these materials.
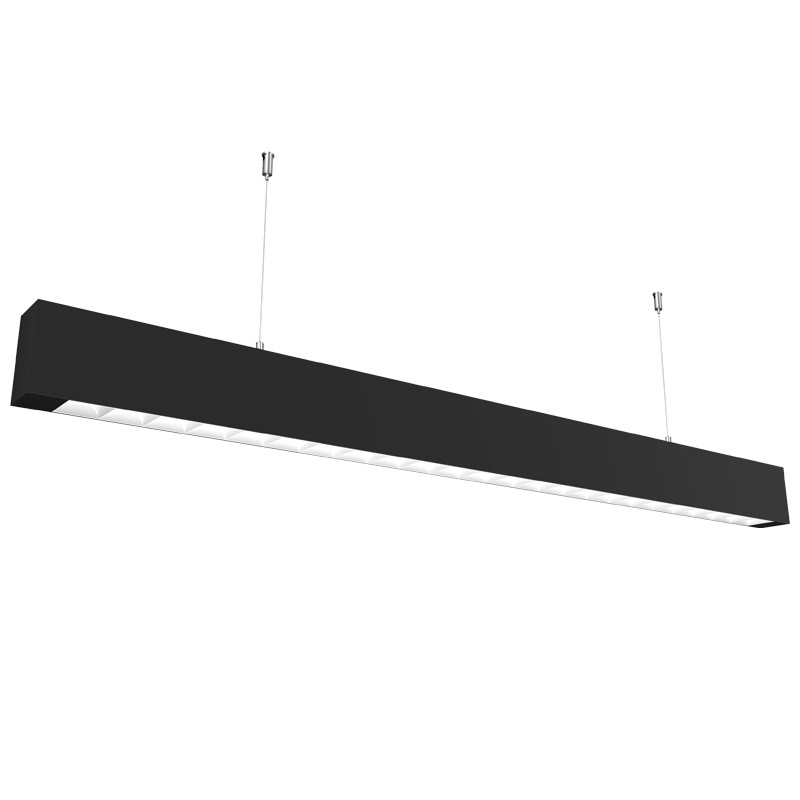
While indirect materials may not be directly related to the production of a company’s products, they can significantly impact its bottom line. Proper usage and handling of indirect materials are essential for reducing waste and preventing accidents. Companies should train employees to properly use and handle indirect materials to ensure safety and minimize waste. In the construction industry, indirect materials such as safety gear, small tools, and administrative supplies are vital for project completion. These materials support the workforce and help maintain safety standards on-site.
Proper inventory management is crucial for effective production processes. By distinguishing between direct and indirect materials, companies can better manage inventory levels and avoid stockouts. By properly managing indirect materials, businesses can optimize their procurement processes, reduce costs, and improve overall operational efficiency. Many focus on indirect materials as businesses strive to optimize their operations and improve their bottom line. While not directly involved in the production process, these materials support business activities.
For example, a company with too many cleaning supplies in stock may expire or become obsolete before use. By reducing the inventory on hand, companies can avoid these types of waste and save money. Direct materials are typically ordered based on specific production needs, while indirect materials are often ordered regularly to maintain the facility.
In today’s competitive business landscape, understanding the importance of indirect materials and implementing effective management strategies is crucial for long-term success. With the information and insights provided in this blog, readers can make informed decisions to optimize their indirect material management and achieve their business goals. For example, if cleaning supplies are ineffective, they can lead to unsanitary conditions that can cause illness or injury. Similarly, if maintenance tools are not properly calibrated or maintained, they can pose a risk to workers. Training employees on properly using and handling indirect materials can help reduce waste and prevent unnecessary expenses. By educating employees on best practices for using materials and managing inventory, businesses can ensure everyone is on the same page and working toward the same goals.
Either the material does not belong to the end product or has an insignificant cost. For example, in the former case, the screws might be useful in the machines used to produce cars. In other words, it can be seen that these are the costs that are mainly incurred holistically within the production or manufacturing process, but they are not exclusive to a certain product.